Himeji Plant
Plant Manager | Kazuto Okazaki, Executive Officer |
---|---|
Location | 992-1 Aza-Nishioki, Okinohama, Aboshi-ku, Himeji, Hyogo |
Number of employees | 1,258 (including research center) (As of March 31, 2024) |
Products | Acrylic acid, acrylates, maleic anhydride, superabsorbent polymers, resin modifiers, electronic information materials, De-NOx catalysts, dioxins decomposition catalysts, and other products |
FY2023 Results of RC Activities
Occupational safety and health | One injury with loss of workdays, five injuries without loss of workdays (including contractors) |
---|---|
Process safety and disaster prevention | Zero Class A process safety accidents, one Class B process safety accident |
Environmental protection | Implemented measures for energy conservation amounting to about 4,800 kL/year (crude oil equivalent) |
In terms of occupational safety and health, we began a new near miss analysis that incorporates a Safety II approach that focuses on what is currently working well. We are also developing a compliment activity, which includes voting for employees who take safe behaviors such as thinking before you act, pointing and calling, and holding the handrail when stepping on stairs. These initiatives aim to promote positive awareness of safety action throughout the plant to help establish a safety culture.
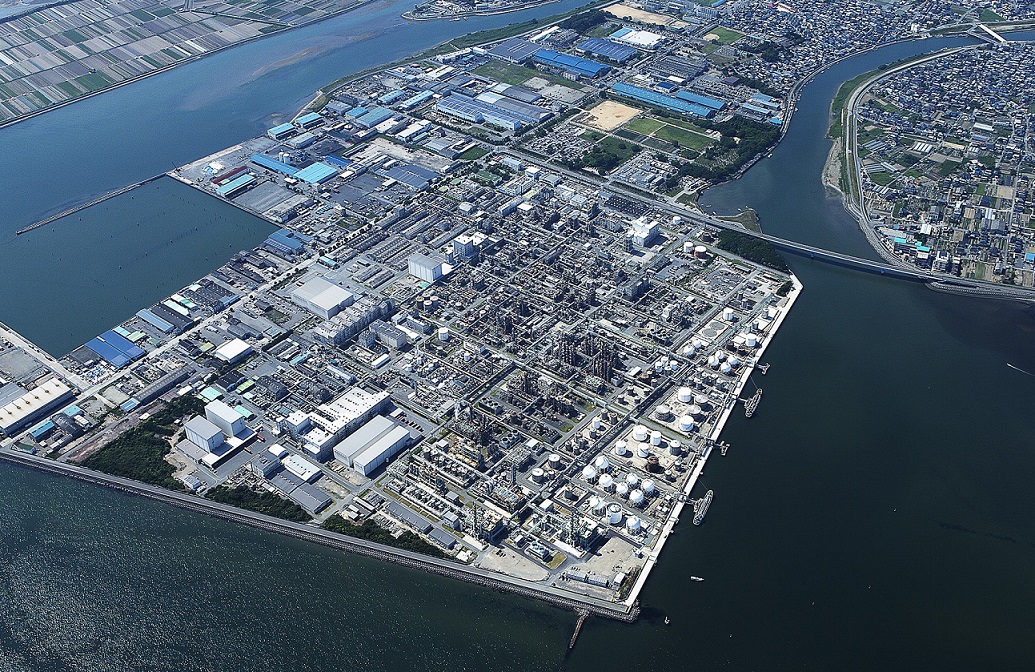
In terms of process safety and disaster prevention, in light of the repeated occurrence of accidents such as leakage of hazardous materials, all employees at the Himeji Plant are taking this issue personally, and we are promoting an initiative called “Safety Reform 2025” with the aim of reforming safety awareness and the safety culture. We will combine the thoughts and actions of all employees to build a safe and stable plant by learning from past accident within the Company and from other companies, reviewing procedures for handling hazardous materials, promoting speaking up, asking questions, watching over others, and holding interdepartmental meetings.
Regarding environmental protection, in response to the Plastic Resource Circulation Act, we have added product residues and plastic pallets, which were previously disposed of as waste, to our list of items for material recycling, and we have repurposed over 200 tons of waste plastic for new uses. We will continue to respond flexibly to changes in society and work together to think and act in order to build a manufacturing plant that is trusted by society.
Education using an explosion safety simulation equipment
Incorrect handling of organic solvents and powders used at the Himeji Plant could lead to a serious accident. However, traditional education on how to prevent such accidents was mainly classroom learning, which had not always been sufficient. Therefore, in order to enhance hazard prediction skills and safety awareness, we introduced an explosion safety simulation equipment, which simulates an explosion caused by static electricity, allowing trainees to experience the fear and danger of an accident firsthand. During new employee training, all employees took part in the simulation training with a serious attitude, and some even commented that they could feel the danger of the substances handled in their work. It even received a great response in environment and safety exchange meetings with Group companies in Japan. We will continue to enhance education to improve safety awareness and promote daily activities to ensure safe and stable production.
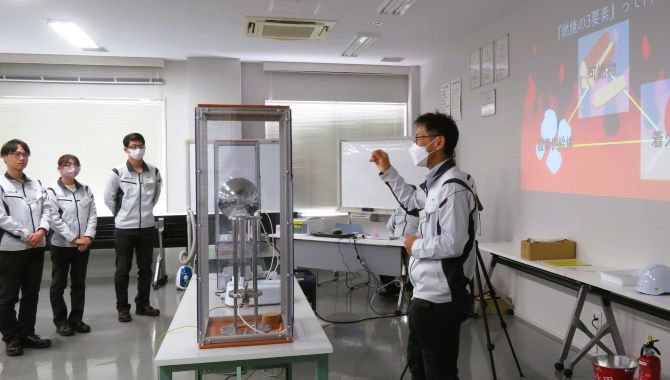
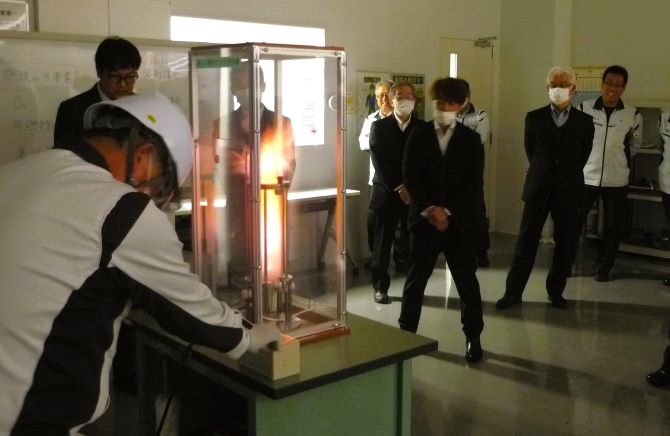
Education using an explosion safety simulation equipment
Using an AI scheduler to optimize SAP production plans and reduce waste
SAP production plans are formulated taking into account sales volume, inventory volume, and productivity, but because there are many types of products and it is heavily dependent on the experience of the person in charge, optimization has been very difficult. In addition, reducing production loss has been a significant challenge, because this loss is inevitably caused by changing product type and is treated as waste. Therefore, we introduced a system using AI to automatically generate optimal production plans based on data science. This enables us to accurately predict the product shipping timing and inventory volume, thereby reducing the number of product type changeovers and a significant amount of waste. In addition, we were able to save energy and reduce CO2 emissions.
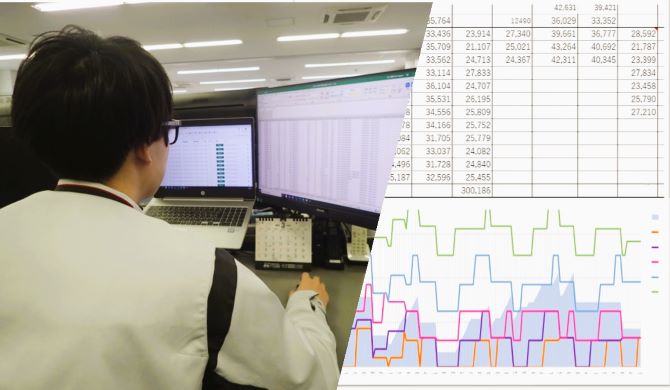
Working with AI scheduler
TopicsParticipation in “Demand Response” contributes to stabilizing the balance between supply and demand of electricity
“Demand Response (DR)” has been attracting attention as a method of adjusting the supply-demand balance of electric power as the introduction of renewable energy sources, which are unstable in terms of power generation, expands. As one of its social contribution activities, Himeji Plant has concluded a contract with a DR aggregator* and has been participating in DR on an ongoing basis since FY2021. When the supply-demand balance of electric power becomes tight due to extreme heat, severe winter, or bad weather, the plant will contribute to stabilizing the supply-demand balance of electric power by reducing the amount of power received from the power grid based on requests from the DR aggregator, utilizing excess power generation capacity.
*DR aggregator: A business operator that aggregates multiple consumers and adjusts supply and demand
Plant Data
Trends in Energy Consumption and Intensity
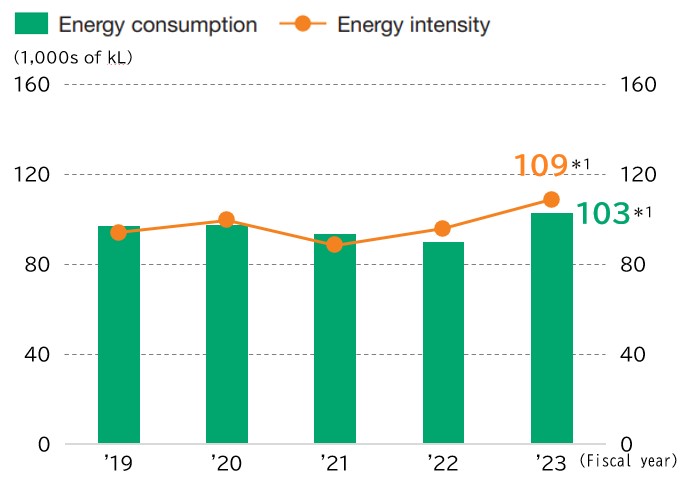
Trends in CO₂ Emissions and Intensity
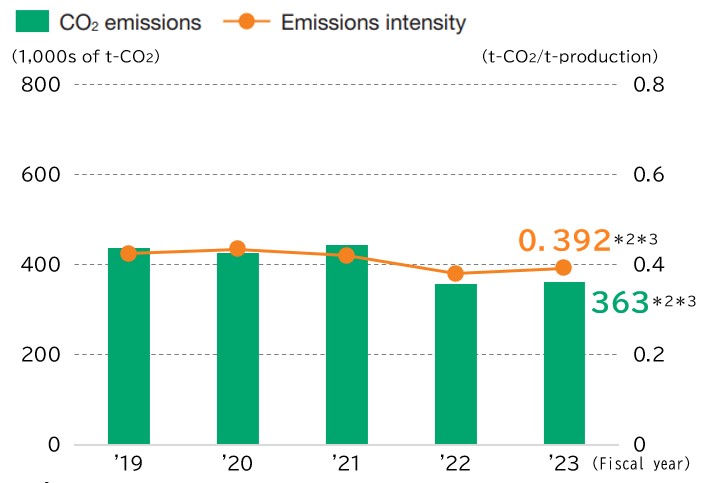
*3 Due to the revision of the Act on Promotion of Global Warming Countermeasures (Global Warming Countermeasures Act), the calculation method has been revised from the fiscal 2023 results.
Trends in Emissions of SOx, NOx, and Dust
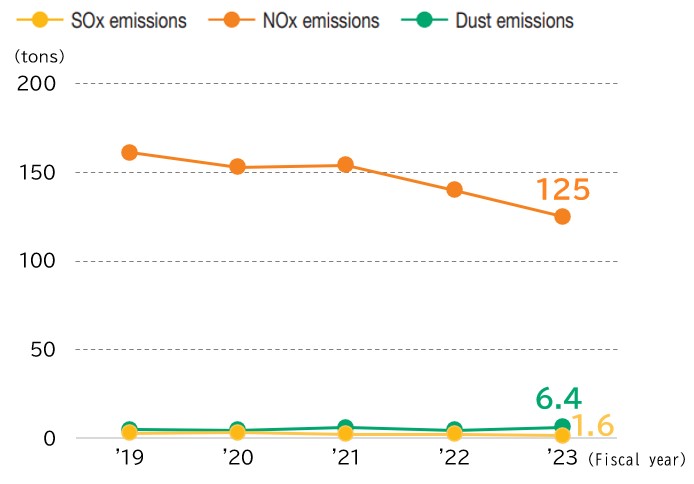
Trend in COD of Wastewater
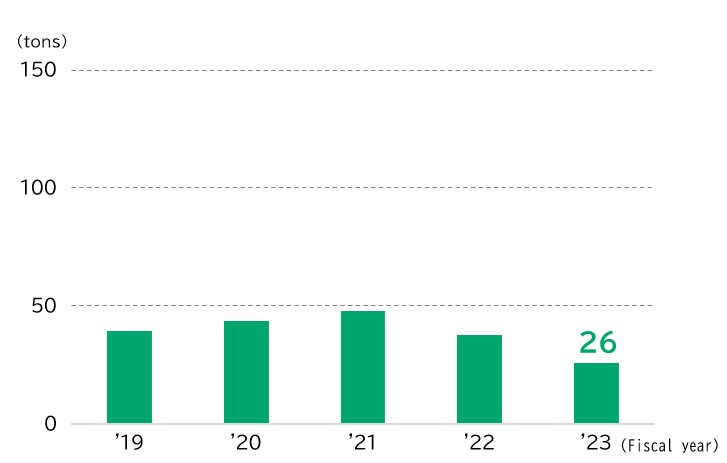
Trends in Amount of Waste, Recycled Waste, and Waste for Final Off-site Landfill Disposal
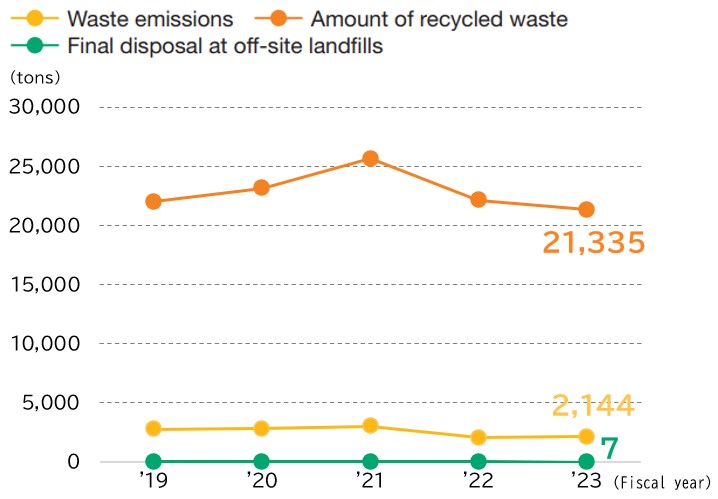
Trend in Emissions of Substances Subject to the PRTR Law
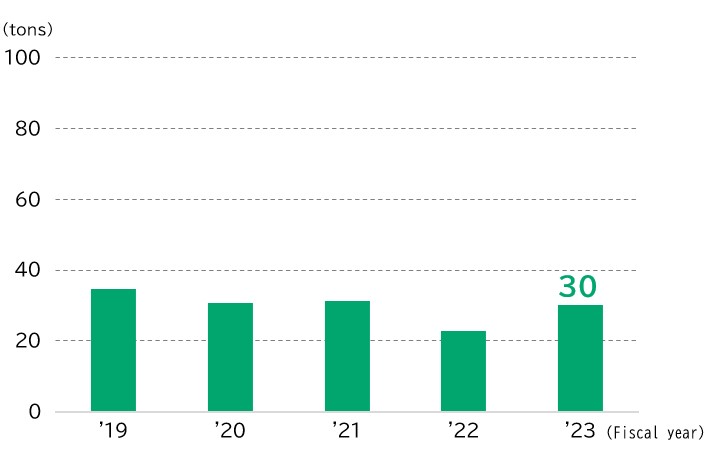