Tackling Climate Change
Click here for the TCFD report.
Promoting Greenhouse Gas (GHG) Emissions Reduction
Formulating a roadmap for reducing GHG emissions
Nippon Shokubai formulated a roadmap for reducing GHG emissions by 2050 in terms of the “strategic transformation for environmental initiatives,” one of the “three transformations” set out in “TechnoAmenity for the future,” the Nippon Shokubai Group long-term vision published in April 2021.
Regarding our GHG emissions reduction target for FY2030, the final year of our long-term vision, we set a target of reducing our GHG emissions in Japan, which constitute roughly 70% of Group-wide emissions, by at least 30% from FY2014 levels by FY2030.
We have purchased carbon-neutral city gas since FY2022, and increased the amount of renewable energy introduced in FY2023. Our GHG emissions of FY2023 in Japan, including those offset by carbon-neutral city gas, amounted to 714,000 t-CO2e,*1 a 15%*1 reduction from FY2014 levels. We are currently considering setting targets for GHG emission reductions including Group companies outside Japan.
The calculation of GHG emissions and energy consumption has undergone third-party verification (see Third-party Verification Report on GHG).
Roadmap for Reducing GHG Emissions by 2050
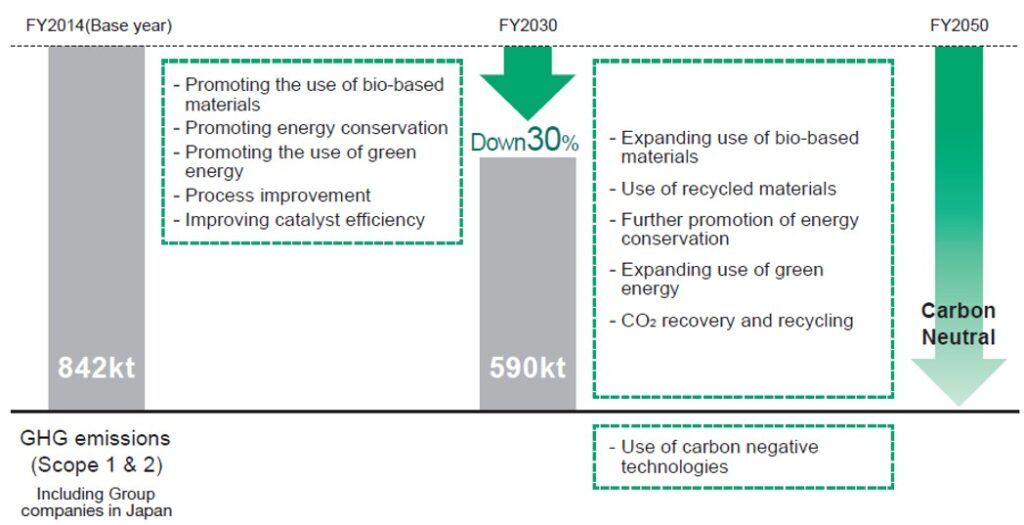
Trend in GHG Emissions (in Japan)
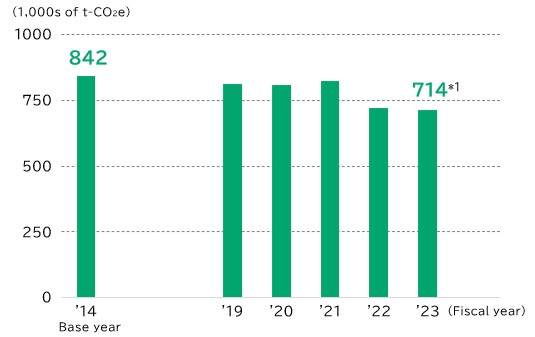
*1 Including a carbon credit offset of 62,000 tons of CO2 emissions (7.3% reduction from the FY2014 level) due to the purchase of carbon-neutral city gas
Reducing energy consumption and CO2 emissions
Our RC Promotion Committee, which is chaired by the Company President, formulated a Medium-Term RC Basic Plan based on the targets set out in the action plan of the Japan Chemical Industry Association (JCIA) for achieving a low carbon society. On the basis of this plan, each of our plants takes action to mitigate climate change under the leadership of the committees responsible for promoting energy conservation activities and a reduction in CO2 emissions.
In FY2023, although energy-saving activities progressed, the energy consumption intensity deteriorated due to declining production volumes of energy generation products as well as products with relatively low energy consumption intensity. In addition, a decrease in production volume contributed to the worsening of CO2 emission intensity, but CO2 emissions were reduced partly due to the use of carbon-neutral city gas.
In FY2021, we started solar power generation (on-site PPA) at the Himeji Plant. In addition, we promote energy conservation activities through the collection of waste heat and the introduction of a co-generation system. We also collect part of the CO2 generated in the manufacturing process and sell it as liquefied carbon dioxide to reduce CO2 emissions.
Employee’s VoiceIntroducing an advanced process control system for energy savings
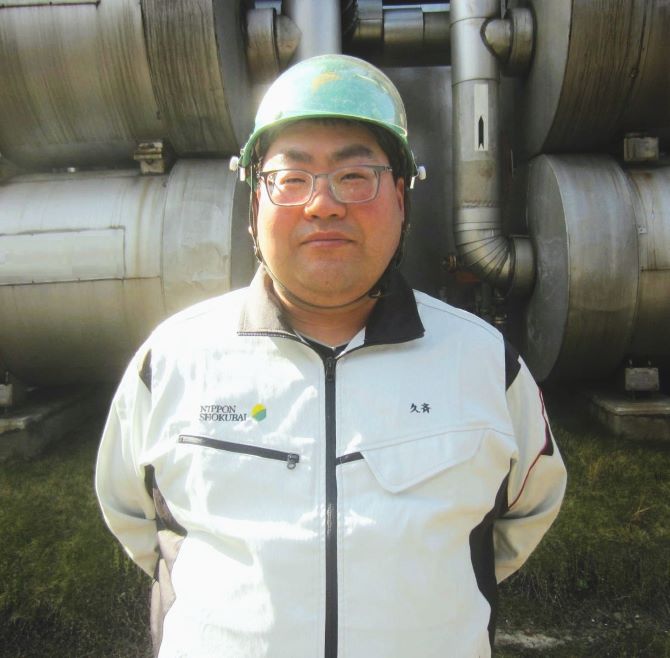
Production No. 3 Section, Kawasaki Plant
At the Kawasaki Plant, we are working to enhance productivity and save energy through the use of digital transformation (DX). As part of this project, we introduced an advanced process control system at the ethylene oxide plant.
The advanced process control system uses DMC* software to monitor and predict process operation data, and simultaneously operates multiple measuring instruments to ensure optimal conditions based on a constructed operation model. It reduces operating fluctuations compared to plant operations performed by an operator. For example, processes that must be maintained at a specified temperature or higher traditionally required excessive heating to account for fluctuations, but the advanced process control system optimizes the heating volume (by reducing excessive heating), thereby enabling energy savings.
In cooperation with the Technology Department, I selected the measuring instruments to be part of the advanced process control system and explained the details of processes to a system development company. I also performed step response tests on actual manufacturing equipment and took on the role of obtaining actual manufacturing equipment data to be used to build an operation model. We conducted test runs on an operating plant, carefully collecting data with the system development company over several months while making sure not to adversely affect production, and successfully implemented the system. Currently, we are continuing initiatives to deepen the understanding of the system by establishing work procedures, creating educational materials for advanced process control operations, and educating operators.
By introducing this system, we have saved the crude oil equivalent of approximately 900 kL in FY2023. We are currently working to expand the scope of application of the system to promote further energy savings.
* DMC (Dynamic Matrix Control): one of the model predictive control methods
Fluorocarbon emission control
The Act on Rational Use and Proper Management of Fluorocarbons, which covers the entire lifecycle of fluorocarbons from production to disposal, went into effect in April 2015, and regulations for disposing of certain equipment were further tightened in April 2020.
As a manager of Class I specified products, the Company conducts the legally mandated simple inspections and routine inspections according to plans. Additionally, our calculations of leaked fluorocarbons in FY2023 revealed leakage of 40 t-CO2e from the Himeji Plant, 984 t-CO2e from the Kawasaki Plant, and 1,088 t-CO2e Company-wide. We intend to make efforts to reduce leaked fluorocarbons—an activity that facilitates climate change mitigation—by intensifying inspections and maintenance, upgrading to equipment that uses coolants with low global warming and ozone depletion potential, and properly disposing of equipment.
Calculations of Leaked Fluorocarbons in FY2023
(t-CO2e)
Himeji Plant | Kawasaki Plant | Others | Entire company |
---|---|---|---|
40 | 984 | 65 | 1,088 |
Promoting for the Reduction of the CO2 Emissions Resulting from Our Entire Supply Chain
Calculating Scope 3 emissions
The GHG Protocol classifies GHG emissions into three classes: Scope 1, Scope 2, and Scope 3, which are the total GHG emissions attributable to business activities throughout supply chains for all categories.
- Scope 1Direct GHG emissions by the reporting company itself (e.g. fuel combustion, industrial process)
- Scope 2Indirect emissions from the use of electricity, heat, or steam supplied by others
- Scope 3Indirect emissions other than Scope 1 and Scope 2 (emissions by others related to the company’s activities)
Nippon Shokubai will continue to calculate Scope 3 emissions and explore the possibility of reducing CO2 emissions resulting from all corporate activities.
Trend in Scope 3 Emissions (Data for Nippon Shokubai alone)
(1,000 t-CO2e)
No. | Category | Emissions | ||
---|---|---|---|---|
FY2021 | FY2022 | FY2023 | ||
1 | Purchased goods and services | 1,522 | 1,370 | 1,462 |
2 | Capital goods | 44 | 43 | 49 |
3 | Fuel- and energy-related activities not included in Scope 1 or Scope 2 | 83 | 89 | 97 |
4 | Upstream transportation and distribution | 15 | 13 | 14 |
5 | Waste generated in operations | 8 | 5 | 5 |
6 | Business travel | 0.3 | 0.3 | 0.3 |
7 | Employee commuting | 0.9 | 0.9 | 0.9 |
12 | End-of-life treatment of sold products | 2,111 | 1,884 | 1,798 |
Total | 3,783 | 3,405 | 3,426 |
Initiatives for the reduction of Scope 3 emissions
In order to contribute to the reduction of Scope 3 emissions, the following items will also be strongly promoted.
- Development and expansion of Environmental Contribution Products (products that contribute to the reduction of CO2 emissions when used, etc.)
- Development and dissemination of CO2 recovery and recycling technology (carbon recycling technology)
- Development and social implementation of material recycling and chemical recycling
Internal Carbon Pricing (ICP)
We have implemented internal carbon pricing (ICP) to promote low carbonization/decarbonization in corporate management on February 1, 2023.
In utilizing the ICP, we will raise awareness of Group’s commitment to decarbonization, promoting energy saving, and activate discussion about opportunities/risks concerning to CO2 emission reductions.
This system is accelerating “Strategic Transformation for Environmental Initiatives” of our “three transformations” set forth in our long-term vision.
ICP | ¥10,000/t-CO2 Shadow price set with reference to domestic and international carbon prices. |
Method of application | The costs will be calculated using ICP based on a change of CO2 emissions and used as a criterion for investment decision. |
Range of application | Nippon Shokubai Group |
GHG Scope | Scope 1 & 2 |