Process Safety and Disaster Prevention
All Nippon Shokubai employees engage in various activities to ensure safety based on our Safety Philosophy, “Safety takes priority over production.”
Basic Approach to Safety Issues
We have incorporated the lessons learned from the accident at the Himeji Plant in 2012 to reinforce our basic approach to safety issues. We have clarified our Safety Philosophy, Safety Oath, and the safety management principles presented below, as well as the roles of the company at each organizational level, and are ensuring that all employees stay fully informed.
Principles for safety management
The Company’s “Rules for Safety Management” set out the basic principles for safety management, guidelines for manufacturing activities, and more, which we put into practice.
Excerpt from basic principles for safety management
(1) Ensure safety based on our Safety Philosophy, “Safety takes priority over production.”
Guidelines for manufacturing activities
(1) When you detect anything out of the ordinary during operations, immediately shut down operations. You are not responsible for the consequences of the shutdown.
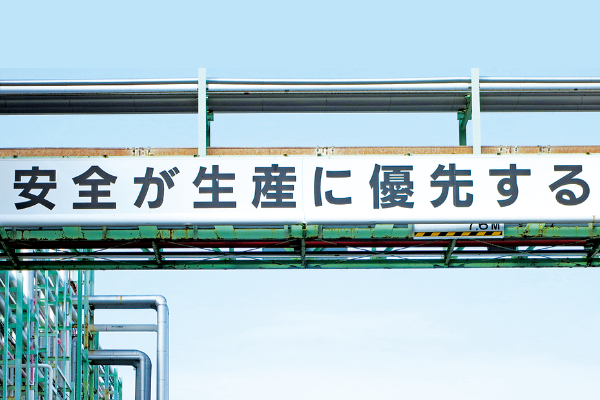
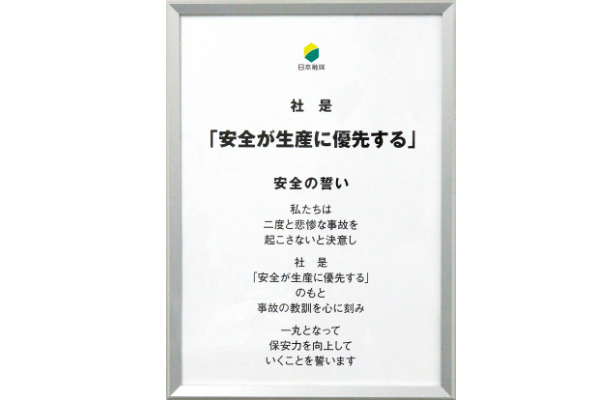
Promotion System
Targets and Results
FY2023 targets | FY2023 results | FY2024 targets |
---|---|---|
Class A process safety accidents: 0 Class B process safety accidents: 0 | Class A process safety accidents: 0 Class B process safety accidents: 2 | Class A process safety accidents: 0 Class B process safety accidents: 0 |
In FY2023, we had zero Class A process safety accident but had two Class B process safety accidents. We will continue efforts to prevent process safety accidents while continuously improving safety activities.
Trends in the Number of Process Safety Accidents
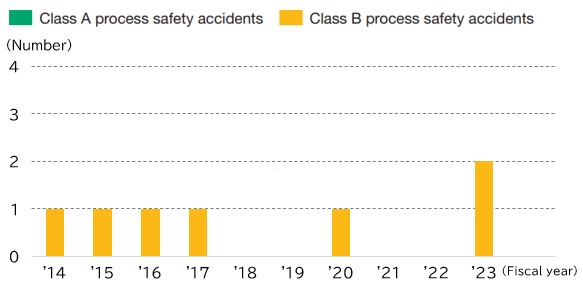
Initiatives
Message from the President on Safety
During a briefing in the days leading to Safety Oath Day in FY2023, the President emphasized that the foundation of the Company’s survival is safe and stable operations, and to continue on this path, it is important for each and every employee to implement basic safety activities and recurrence prevention measures with on a daily basis in the spirit of our Safety Philosophy of “Safety takes priority over production.” During Safe Operation Month (from September 16 to October 15), safety discussions were held at each workplace to discuss what can be done at each workplace to strengthen the culture of prioritizing safety and what one’s own role and responsibilities are.
President’s Plant Visits
Again in FY2023, the President visited both the Himeji and Kawasaki Plants actively to have a lively dialogue with the plant employees on topics including safety.
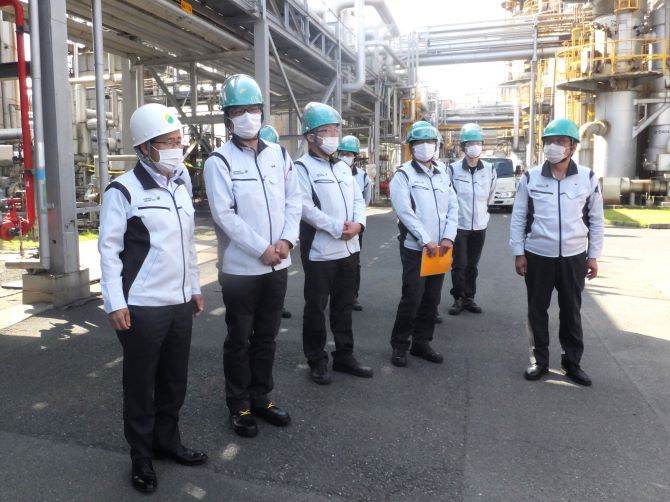
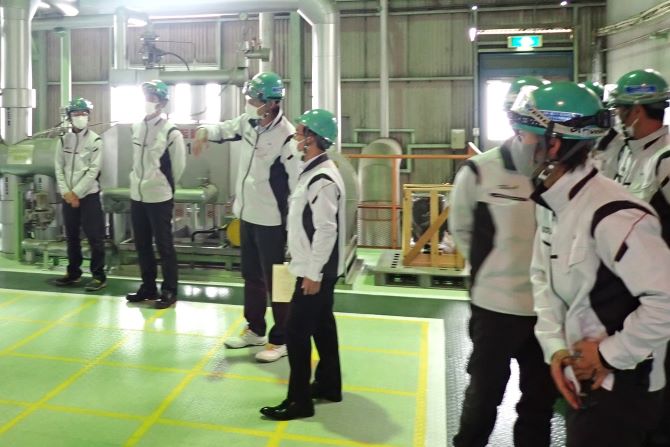
Preventing trouble
Our efforts to prevent trouble include adopting HAZOP as our method of identifying potential risks at plants and systematically implementing it (including both routine and non-routine situations) in addition to consistently implementing change and non-routine work management.
We also implement small group activities—HMI activities at the Himeji Plant and KICS activities at the Kawasaki Plant—to identify deficiencies and promote improvement.
We intend to continue implementing broad-ranging activities to prevent trouble.
Systematically implementing safety measures
When accidents occur, we analyze the causes from various perspectives and implement countermeasures in addition to reflecting and systematically implementing permanent measures for facilities in maintenance plans. We also systematically promote measures to counter the age-related deterioration of facilities.
Seismic countermeasures
In light of our experience with the Great East Japan Earthquake in 2011, we have reviewed and undertaken both technical and non-technical measures to prepare for massive earthquakes and tsunami. We also periodically revise and strengthen the measures.
Regarding existing measures to improve the earthquake resistance of high-pressure gas facilities, we have already verified that our spherical tanks with steel pipe braces and gas holders—critical high-pressure gas facilities in terms of seismic design—satisfy earthquake-resistance standards, and have reported that fact to the relevant administrative agencies. We will also continue to implement earthquake resistant measures for piping in FY2024.
Enhancing education and training
We are striving to enhance training for chemical plant risk management in an effort to strengthen skills and abilities pertaining to safety.
The courses on risk management and other related topics were given in FY2023, as usual, by instructors from the Sanyo Association for Advancement of Science & Technology, in which a total of 51 employees participated.
We also collect and organize “Know-Why” information for use in training to enable trainees at both plants to inherit techniques and understand the basis for procedures and rules.
We intend to continue internal and external training while incorporating the views of our employees in an effort to improve their knowledge and awareness of safety.
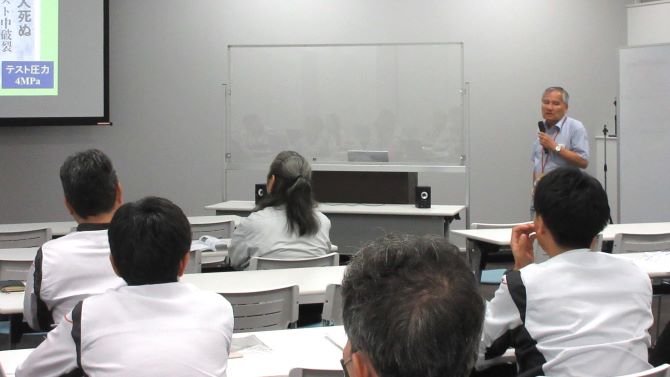
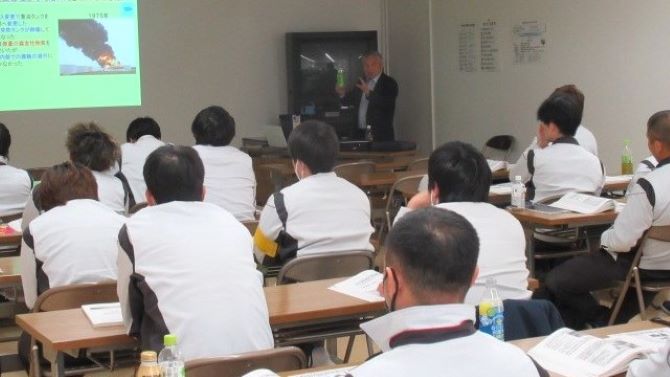
Verification of safety management activities
In FY2023, as in previous years, the management conducted RC inspections and checked the safety management activities for the Himeji and Kawasaki Plants.
Head Office auditors chaired by the executive officer in charge of the Responsible Care Division also conducted safety audits and verified the implementation status and effectiveness of the safety management system.
Certified high-pressure gas plants
The Chidori and Ukishima Plants of the Kawasaki Plant were certified by the Ministry of Economy, Trade and Industry in 1989 and 1991, respectively, as entities capable of conducting completion and safety inspections for high-pressure gas certification, and each undergoes screenings for renewal every five years.
This certification allows plants with outstanding voluntary safety systems to continuously operate high-pressure gas manufacturing facilities and conduct their own safety inspections. The certification of the Ukishima Plant was renewed in February 2024.
Improving emergency drills
Each plant has established a disaster risk reduction system and systematically conducts emergency drills for different types of disasters and accidents each year.
In FY2023, as in the previous year, the emergency drills were conducted at each plant.
By reflecting the issues identified in disaster prevention drills into subsequent drills, we revise and strengthen our disaster risk reduction system as well as education and training.
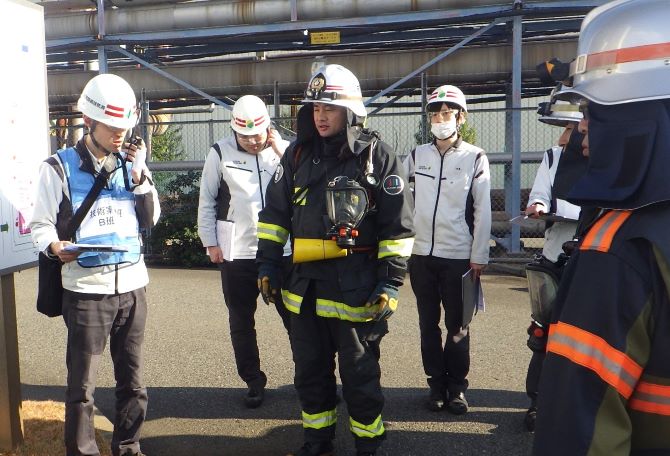
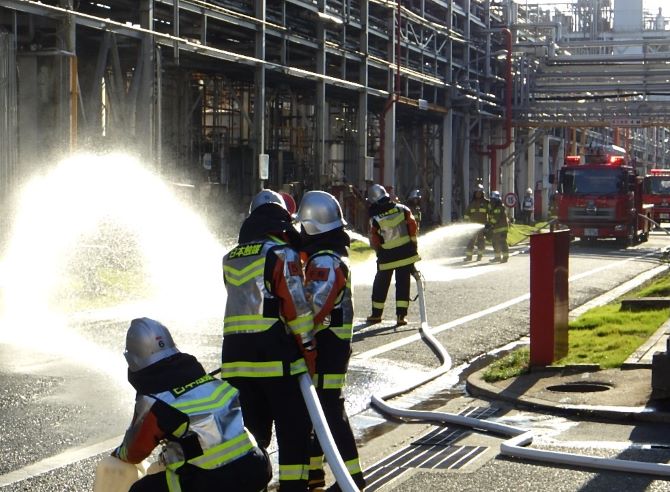
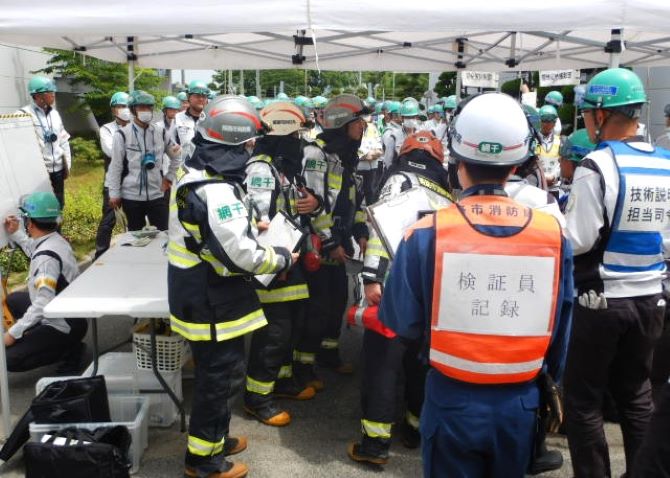
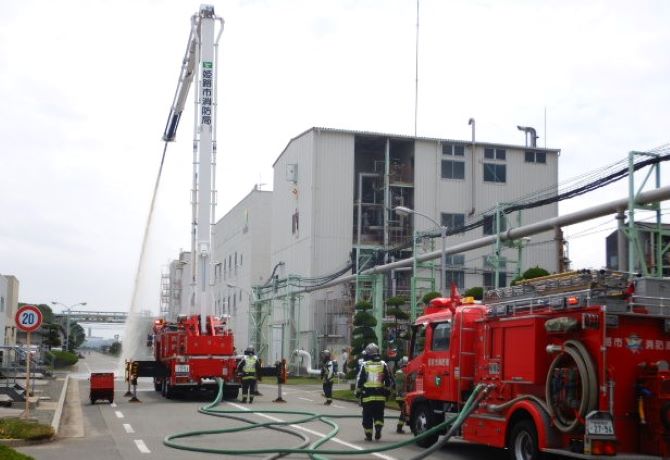
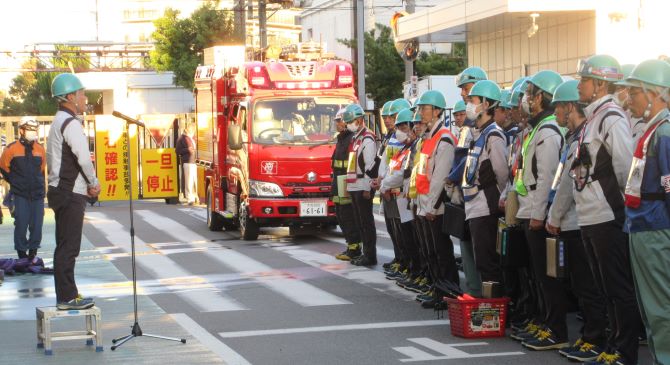
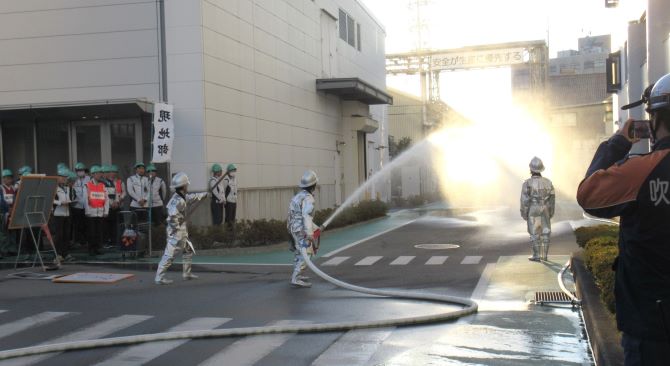
Strengthening the culture of prioritizing safety
To strengthen the culture of prioritizing safety, it is essential to recognize that safety is not something given by others, but something we must think about and earn on our own, and to reflect this in the organization and our own actions. Both plants are engaging in distinct initiatives in an effort to strengthen the culture of prioritizing safety.
Preserving memories of accidents
To prevent memories and lessons learned from the 2012 accident from fading and to demonstrate our determination to avoid similar accidents, we held another Safety Oath Ceremony in front of the Safety Oath monument at the Himeji Plant in FY2023 to recommit ourselves to improving our safety capacity.
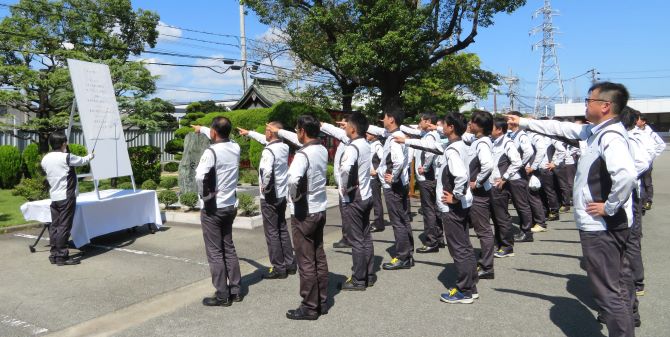
Commendations
At the 52nd Hyogo High Pressure Gas Safety Managers’ Convention, an employee of our Himeji Plant received as an excellent high-pressure gas safety manager.
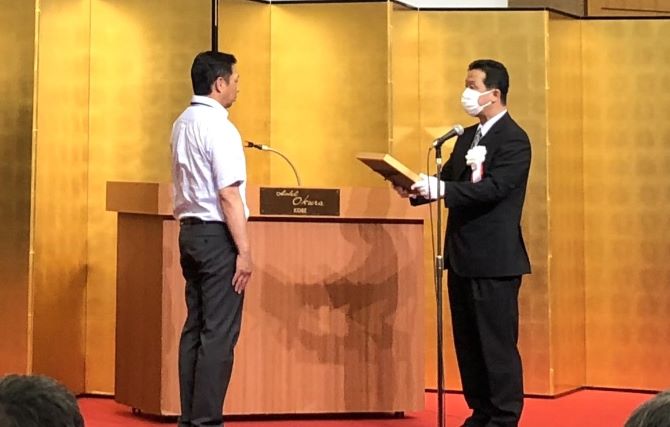