Kawasaki Plant
Plant Manager | Koji Takeda, Executive Officer |
---|---|
Location | Chidori Plant 14-1 Chidori-cho, Kawasaki-ku, Kawasaki, Kanagawa Ukishima Plant 10-12 Ukishima-cho, Kawasaki-ku, Kawasaki, Kanagawa |
Number of employees | 367 (As of March 31, 2024) |
Products | Ethylene oxide, ethylene glycol, ethanolamine, polyethyleneimine, secondary alcohol ethoxylates, polymers for concrete admixture, acrylic acid special ester, and other products |
FY2023 Results of RC Activities
Occupational safety and health | Six injuries with loss of workdays, one injury without loss of workdays (including contractors) |
---|---|
Process safety and disaster prevention | Zero Class A process safety accidents, one Class B process safety accident |
Environmental protection | Implemented measures for energy conservation amounting to about 2,000 kL/year (crude oil equivalent) |
In terms of occupational safety and health, due to the occurrence of five employee injuries with loss of workdays (including chemical burns and cuts), we reviewed the safety activities at our plant during the period, identified areas where near miss analysis reports or those countermeasures related to the injuries were insufficient, implemented these additional countermeasures, and conducted thorough safety checks before work at actual job sites. As individual countermeasures, we implemented thorough prevention of similar problems by correcting issues in work management and work methods.
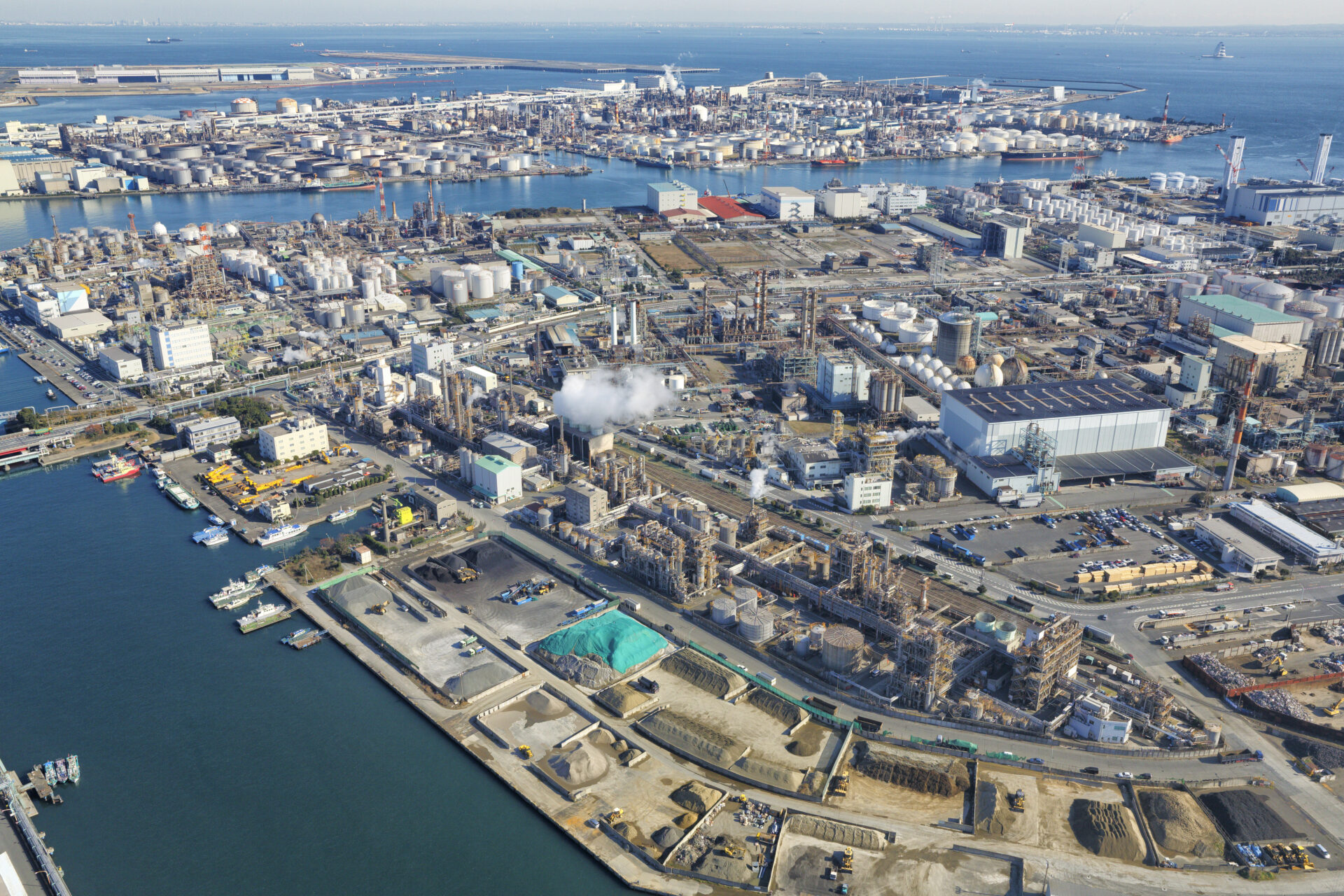
In the area of process safety and disaster prevention, although one Class B process safety accident (leakage) occurred, we implemented thorough prevention of similar problems by ways such as increasing the number of devices for detecting equipment abnormalities.
In terms of environmental protection, we promoted energy-saving measures such as introducing an advanced process control system to predict fluctuations in each process and provide simultaneous control (refer to the Employee’s Voice). We also continuously made our efforts in response to the PRTR Law such as with boron recovery.
We intend to continue promoting RC initiatives to incorporate cutting-edge technology and make our plant safer and more trustworthy.
Supporting training of younger operators at group companies
The Kawasaki Plant hosted a two-day face-to-face group training for younger operators in their first to fourth years at Nippon Shokubai Group companies in Japan. This was started as a part of Nippon Shokubai educational support activities in response to common issues regarding training system and a shortage of instructors among Group companies in Japan. The instructors, who are training center staff with extensive experience in plant operations and regularly provide operator training, used DVD footage and cutaway models of equipment to provide classroom training on safety, equipment, and past issues as well as hands-on training on-site to verify the operation of safety devices on a tank.
We will continue to enhance the skillset of younger employees in cooperation with Group companies in a training setting.
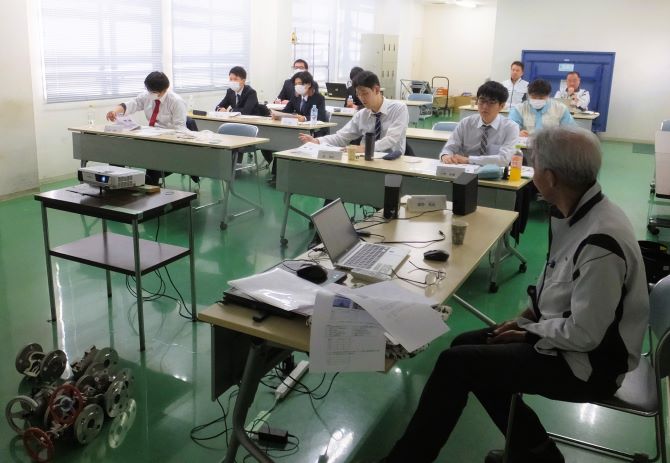
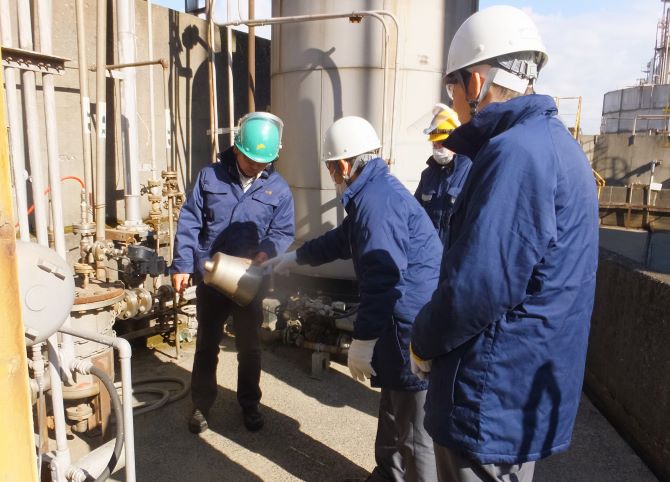
Introduction of HAZOP-LOPA
In an effort to further enhance risk assessment related to the hazard identification in processes at the Kawasaki Plant, we are introducing the HAZOP-LOPA procedure. LOPA is a method used to quantitatively determine whether sufficient measures are in place for scenarios where accidents can occur and whether a risk is acceptable. Specifically, it reduces the probability of an accident to an acceptable level by putting various safety measures into place. To achieve this, we formed an in-house working team. First, as preliminary education necessary for consideration, we asked Professor Takagi of Systems Safety Consulting Ltd. to act as a consultant, and took a safety engineering lecture. In the future, members who mastered the LOPA risk assessment method will act as promoters and will assess risks in each production section with the aim of introducing LOPA in FY2026.
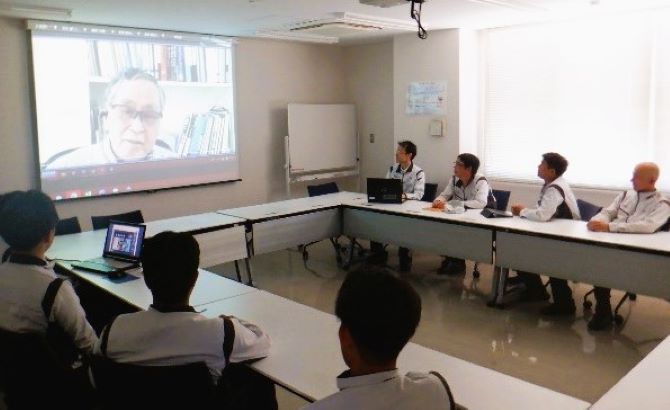
Plant Data
Trends in Energy Consumption and Intensity
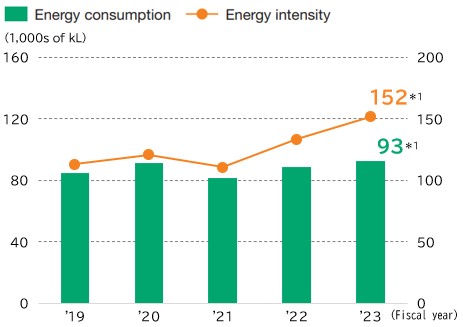
Trends in CO₂ Emissions and Intensity
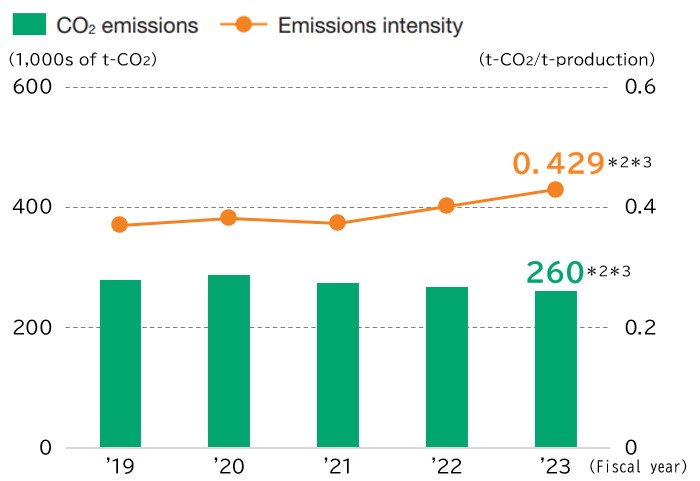
*3 Due to the revision of the Act on Promotion of Global Warming Countermeasures (Global Warming Countermeasures Act), the calculation method has been revised from the fiscal 2023 results.
Trends in Emissions of SOx, NOx, and Dust
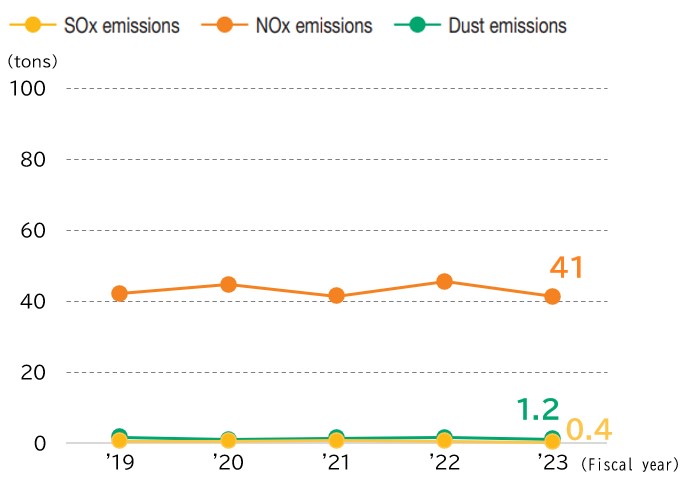
Trend in COD of Wastewater
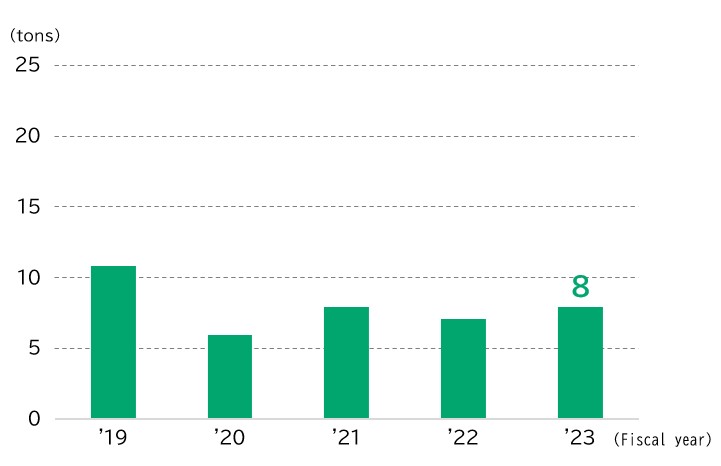
Trends in Amount of Waste, Recycled Waste, and Waste for Final Off-site Landfill Disposal
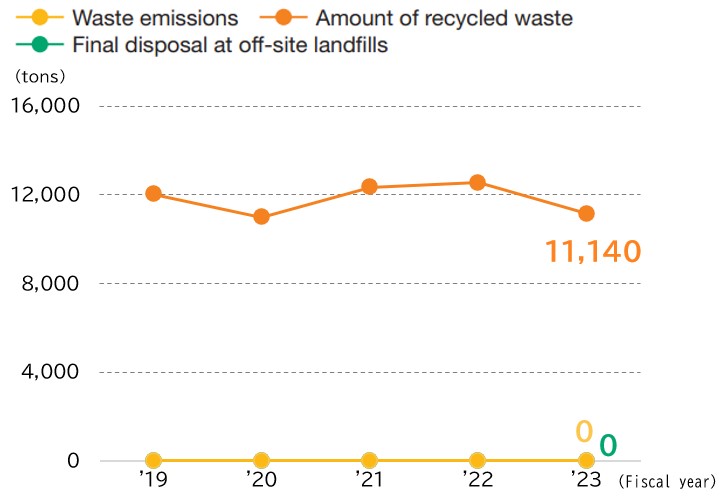
Trend in Emissions of Substances Subject to the PRTR Law
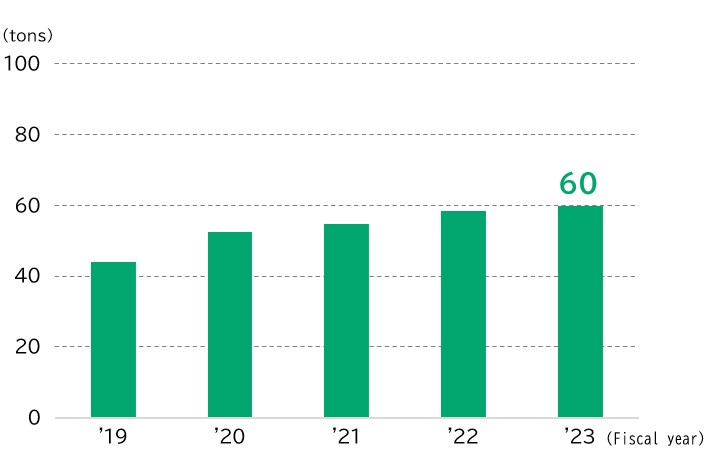