Himeji Plant
Plant Manager | Tokihiro Yokoi, Executive Officer |
---|---|
Location | 992-1 Aza-Nishioki, Okinohama, Aboshi-ku, Himeji, Hyogo |
Number of employees | 1,235 (including research center) |
Products | Acrylic acid, acrylates, maleic anhydride, superabsorbent polymers, resin modifiers, electronic information materials, De-NOx catalysts, dioxins decomposition catalysts, and other products |
Contact | TEL+81-79-273-1131 FAX+81-79-274-3723 |
FY2022 Results of RC Activities
Occupational safety and health | Zero injuries with loss of workdays, four injuries without loss of workdays (including contractors) |
---|---|
Process safety and disaster prevention | Zero Class A and Class B process safety accidents |
Environmental protection | Implemented measures for energy conservation amounting to about 4,800 kL/year (crude oil equivalent) |
FY2022 marked the 10th anniversary of the explosion and fire at the acrylic acid production facilities. We held a lecture meeting on safety with Dr. Masayoshi Nakamura, an accident investigation committee member, as the lecturer. This lecture meeting provided employees with an opportunity to think anew about what we should do to pass on the lessons of the accident to future generations and prevent such an accident from recurring.
As for occupational safety and health, the Himeji Plant has continued to strive to thoroughly implement the practice of basic safety behavior (think before you act, pointing and calling, and hold the handrail when stepping stairs). As a result, the number of industrial injuries decreased by half from eight in the previous year to four, and there were zero injuries with loss of workdays.
Regarding environmental protection, we provide education to employees from various angles to strengthen our activities to achieve carbon neutrality. As part of such efforts, a lecture was given by a researcher of JAXA (the Japan Aerospace Exploration Agency) with the theme “Earth Seen from Space.”
In addition, in an effort to promote smart safety, we are working to advance the use of new inspection technology for facilities. For example, a drone is used to check facilities and equipment, producing results.
The Himeji Plant will continue to strive to provide maximum value for customers by enhancing the resilience of each member of the plant.
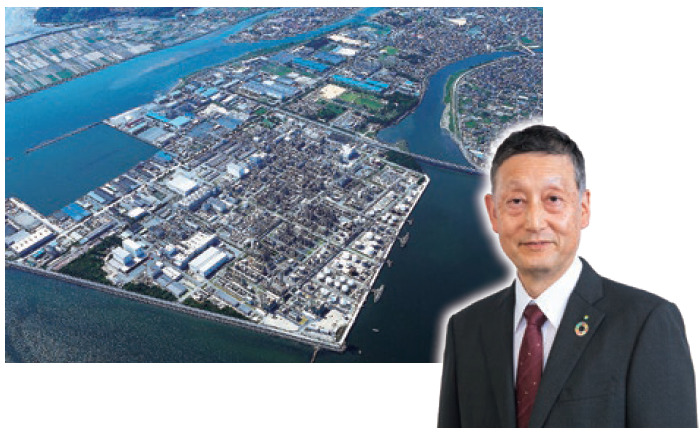
Hands-on learning using VR safety experience equipment
In FY2022, the Himeji Plant provided hands-on safety education using VR (virtual reality). This education program, which is designed to enhance employees’ awareness of safety through firsthand experience, has recently been introduced as a new safety education method by many companies in the manufacturing industry.
This time, we introduced VR contents for one month through a subscription system to enable employees to have virtual-reality experiences with various types of injuries and accidents using a three-axis VR simulator, such as falling from a height, being caught in machinery, a fire outbreak, or a dust explosion. In this education program, 320 employees of the plant participated and gave feedback in a questionnaire, saying things like, “I was able to have a unique experience that was beyond my imagination and that cannot be provided by case study-based education,” and “This experience made me aware of a sense of danger and fear that I didn’t feel before.” The participants’ feedback shows that the purpose of this education program was achieved.
We will consider introducing VR contents that respond to various on-site needs, and expanding VR education to other plants and contractors.
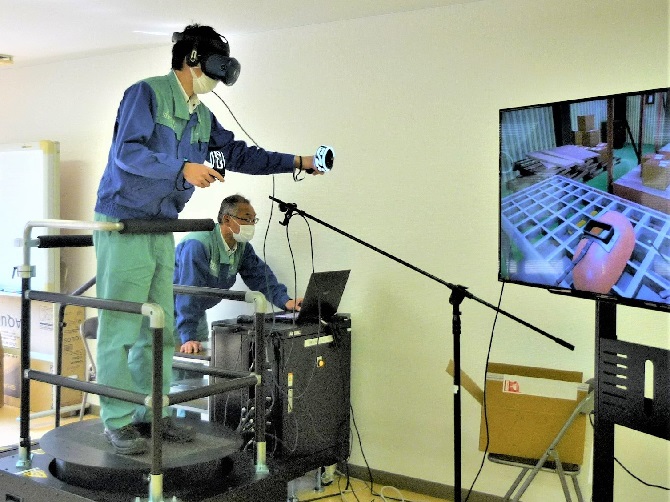
Material recycling of waste plastics
The enactment of the Plastic Resource Circulation Act has accelerated the move toward transition to a circular economy. At the Himeji Plant, plastic containers for raw materials had been incinerated as industrial waste. We have decided to recycle some waste plastics and offer them as raw materials of plastic products. We will continue to contribute to reducing waste, promoting the effective use of resources, and decreasing CO2 emissions by increasing the number of recyclables.
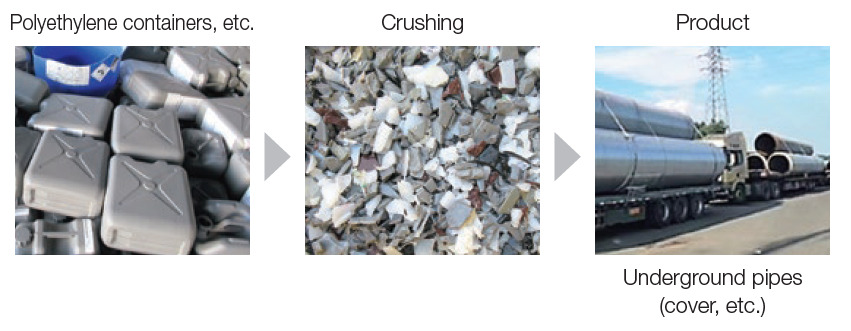
TopicsParticipation in “Demand Response” Contributes to Stabilizing the Balance between Supply and Demand of Electricity
“Demand Response (DR)” has been attracting attention as a method of adjusting the supply-demand balance of electric power as the introduction of renewable energy sources, which are unstable in terms of power generation, expands. As one of its social contribution activities, Himeji Plant has concluded a contract with a DR aggregator* and has been participating in DR on an ongoing basis since FY2021. When the supply-demand balance of electric power becomes tight due to extreme heat, severe winter, or bad weather, the plant will contribute to stabilizing the supply-demand balance of electric power by reducing the amount of power received from the power grid based on requests from the DR aggregator, utilizing excess power generation capacity.
*DR aggregator: A business operator that aggregates multiple consumers and adjusts supply and demand
Plant Data
Trends in Energy Consumption and Intensity
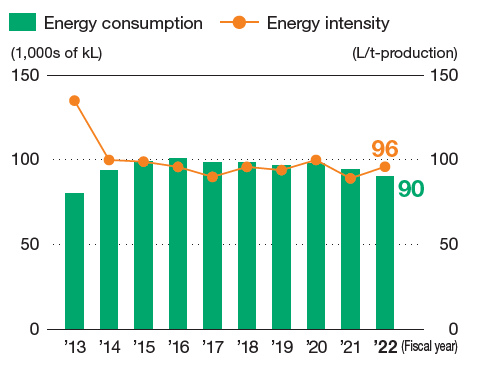
Trends in CO₂ Emissions and Intensity
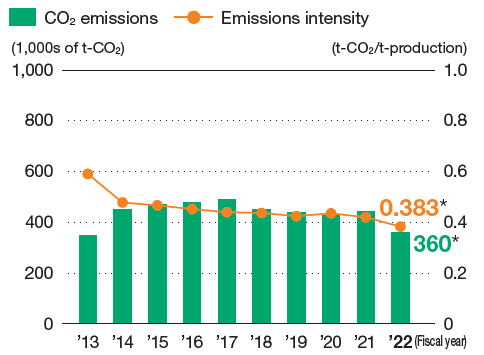
Trends in Emissions of SOx, NOx, and Dust
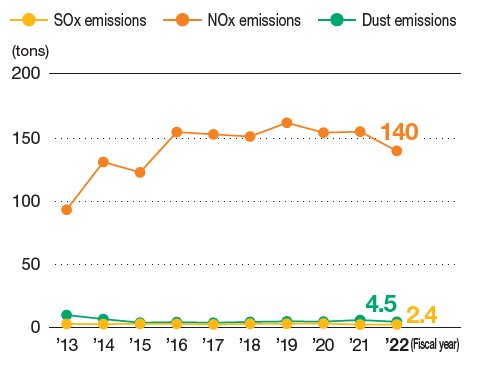
Trend in COD of Wastewater
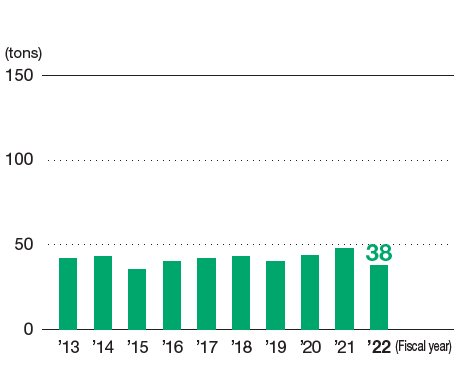
Trends in Amount of Waste, Recycled Waste, and Waste for Final Off-site Landfill Disposal
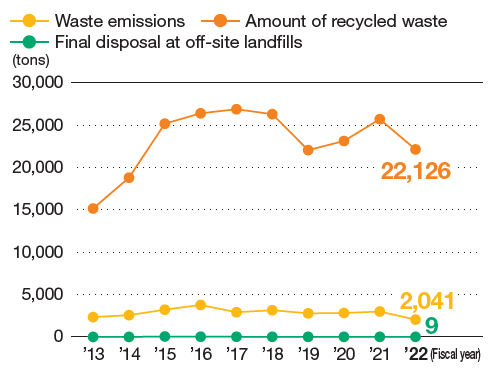
Trend in Emissions of Substances Subject to the PRTR Law
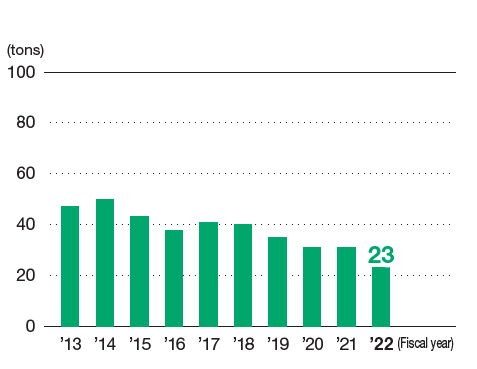